Boiler & HRSG
AKEF provides inspection resources, technology and software to provide the most thorough and comprehensive boiler inspections unlike any other boiler inspection company.
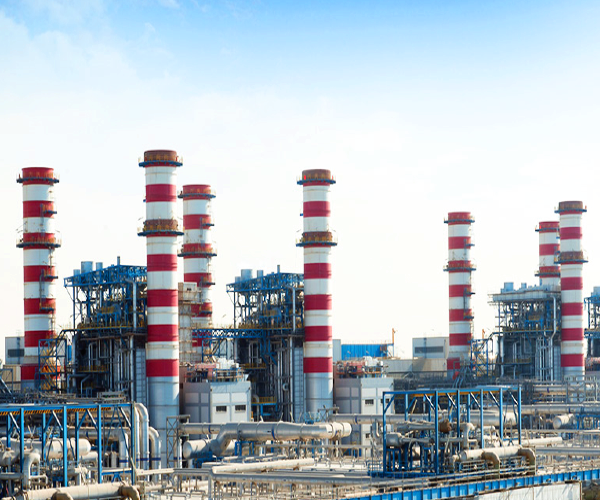
The marine division possesses the capacity to construct, repair, refurbish, and maintain a diverse range of vessels, catering to the varied demands of its clientele. It offers comprehensive engineering and construction capabilities tailored to various types of ships and offshore structures, overseeing all phases of project implementation with meticulous attention to detail and technical proficiency.
Boiler & HRSG Inspection
Engineering Services
AKEF provides inspection resources, technology and software to provide the most thorough and comprehensive boiler inspections unlike any other boiler inspection company. AKEF will provide the plant O&M team the ability to PRIORITIZE and MONITOR corrective action, tracking the status of all repair recommendations. AKEF will provide detailed reports with analysis and predictive failure information to determine an accurate current and future state of their boiler systems, and repair recommendations to help minimize unscheduled (forced) outages.
AKEF ensures its clients a thorough and proper inspection is done on every outage, scheduled or unscheduled. And finally, AKEF ensures repairs are done correctly with no “short cut” that would jeopardize the boiler integrity.
General HRSG Inspection
A visual survey of the general HRSG condition, external casing, internal gas-side mechanical parts and auxiliary equipment. Readily accessible pressure part components are visually inspected. AKEF recommends performing such a general inspection in addition to the basic inspections stipulated by local regulatory requirements. Time frame requirement: 2 – 3 days HRSG accessibility.
Aligning HRSG Inspections for Optimized Availability
In order to prevent forced outages, periodic inspections should be conducted during scheduled outages. This allows the identification of component damage in the earliest stages – when there is still time to schedule a cost-effective repair.
AKEF recommends a general inspection every 1 to 2 years and a more detailed inspection every 3 to 5 years. In order to optimize the overall plant availability, it is important to align these inspections with those of the gas turbine. Therefore, the detailed inspection should coincide with a gas turbine planned outage, e.g. the major or hot gas path inspection.
Detailed HRSG Inspection
Includes all the general inspection steps plus a more detailed visual inspection of all accessible pressure parts. This visual inspection will identify any areas of concern that require subsequent non-destructive examination (NDE) to be performed by AKEF qualified NDE technician. Time frame requirement: 4 – 6 days HRSG accessibility.
Boiler & HRSG Failure Analysis and Engineering Study
Reverse Engineering Philosophy
With more than 20 years of combined experience in managing a wide array of power plant projects, the team in our power generation division is known for delivering impeccable analysis and engineering study for thermal power plants, co-generation power plants, combined-cycle power plants.
Aimed at assisting our clients on the upkeep and O&M (Operation and Maintenance) improvement of their existing fleets, AKEF has developed the capability to service HRSG, IB, FH and coal boiler and provide technical solutions to a wide range of reliability, performance and emission issues.
Our engineer have much experienced, professional engineers can be supplied technical solution when client have issue or problem. AKEF have been able to produce successful results for our clients, meeting, their needs on time and within budget while supplying quality products. AKEF are worked same time zone with client.
Boiler Repair, Retrofit and Maintenance
AKEF provides a comprehensive selection of boiler repair services.
Our Services Include
- Retubing – Partial or complete retubing for watertube and firetube boilers.
- Welding & fabrication – All welding repairs; boiler shell plate, tubesheets, headers, staybolts, handholes / manholes, faceplates, doors, breechings & supports. Pipe fabrication of steam, water & gas piping to ASME and/or API code, X-Ray quality welding.
- Appurtenances, Auxiliaries & Fittings – Safety, blowdown, stop & check valves; gauges, test connections, water column piping, feed pumps, cutoffs, preheaters and backflow preventers.
- Refractory – Firebrick chambers, burner tile, venturi rings, dry oven rings and all refractory repairs.
- Thermal & Acoustic Insulation – Mineral wool blanket & pipe covers, calcium magnesium silicate (CMS) repairs for interior & exterior of boiler.
- Mixing Valves – Rebuilding or replacement
The retrofit and upgrading method to be adopted should be decided based on result of inspection and design review. AKEF can evaluate current boiler or HRSG unit and recommend the right retrofit and upgrade package. AKEF can provide Turn-Key EPC capacity and our service is include:
- PP (Pressure Part) replacement
Furnace wall replacement, Harp/semi harps/ module replacement, Bundle (coil) replacement, Link and Manifold pipe replacement
High energy piping replacement - Air and Gas system replacement
Forced draft fan/ Primary air fan/ Air heater, Duct and casing upgrade - Fuel feeding system replacement
Coal bunker, Coal feeder, Pulverizer, Fuel oil skid, Gas or Oil burner repair and addition - SCR (Selective Catalytic Reduction) and CO system addition and replacement
- Partial tube leakage repair and/or replacement
- Expansion bellows and expansion joint retrofit and upgrade
- MOV/ CV/ Bypass Valves Re-engineering service
- Integral De-superheater (Attemperator) spray valve upgrade
- FCD (Flow Corrective Device) upgrade
- Leak detecting system, Life monitoring system application
- Soot Blower
- Reverse Engineering
Boiler & HRSG Condition Assessment
Our Services Include
Condition assessment services include:
- Remain life assessment and plant life extension
- Metallurgical condition review for high temp. components Thermal degradation, Fatigue, Creep
- Special NDE (PAUT)
- Portable hardness testing
- Metallographic replication
- Failure investigations and material assessment
- Remote visual inspection with borescope
- Pipe support surveys for both hot and cold condition
- High energy piping assessment
- FAC review
- Water chemistry review
- Walk down to identify start-up problems
- Specialized HRSG Condition Assessment
- Header Inspection – Specialized visual inspection technique to inspect headers for signs of Flow Accelerated Corrosion (FAC)
- Phased Array Butt Weld Scanner – Specialized device that uses phased array ultrasonics, combined with an encoded circumferential scan, to check the quality of butt welds on manual TIG / orbital pipe welds with diameters from 1.5″ to 4.5″.
- Water Chemistry Review / Corrosion Assessment – Corrosion risk assessment based on design, historical chemistry readings, applied chemistry concept and operation profile.
- Root Cause Analysis – For specific problems